Creating a raised feature
Creating a raised feature
Use the Raised Feature
option on the Feature Machining panel to
create a raised (male) feature from a selected vector, usually vector text,
which you can then machine using the Feature
Machining toolpath. This toolpath is commonly used in conjunction with
the Machine Relief toolpath.
Using the Feature Machining
panel, you can:
- control whether any central cavity in the vector is removed
or not during the feature machining process; and
- control what edge of the vector the tool meets when cutting
it from the block of material.
To create a raised feature:
- Select the vector from which you want to create a raised
feature.
- In the 3D Toolpaths
area, click the Create Feature Machining
Toolpath
button to display the Feature
Machining panel.
- Select Raised Feature.
- In the Feature Height
box, enter the height of the raised feature that you want to create.
- Select how the tool machines the selected vector:
- Vector at Top Edge —
This option places the selected Feature Tool
in contact with the top edge of the selected vector during the machining
process.
|
Feature tool.
This material is not cut by the feature
tool. |
If this option is selected, you can choose how you want
sharp corners to be machined.
Sharpen At Top — If
selected, sharp internal corners are sharpened at the top of the feature,
provided an angled tool is used.
Sharpen At Bottom — If
selected, sharp external corners are extended and sharpened at the bottom of the
feature, provided an angled tool is used.
- Vector at Bottom Edge —
This option places the selected Feature Tool
in contact with the bottom edge of the selected vector during the machining
process.
|
Feature tool
This material is cut by the feature
tool. |
- In the Feature Allowance
box, enter a value if you want to keep or remove extra material around the
selected vector. This sets the distance between the boundary of the selected
vector and the selected feature tool. Enter a positive value to keep material or
a negative value to remove it.
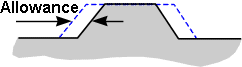
- If the selected vector contains a central cavity that you
want to remove with your selected feature tool, click to select the Clear inner islands option. If you select this
option, any Feature Allowance you have
already created and Overcut Distance that you
specify is ignored by the feature tool you use to machine the raised feature.
If Clear inner islands
is deselected, the feature tool can only remove material inside of a central
cavity as far as the Feature Allowance and
Overcut Distance allow.
- Set the limitations for machining:
- If you want to leave an allowance around the boundary of
the selected vector, including any central cavity that it may contain, select
Use constant allowance around vector.
- If you want to machine around the boundary of the selected
vector, select the Outer vector defines machining
limit option. If the selected vector contains a central cavity, the
cavity is not removed using this option. The Feature
Allowance box is also unavailable.
- Select the machining strategy that you want to use:
- Profile Only — This
strategy enables the cutting tool to make profile passes around the feature you
have selected.
- Area Clear — This
strategy enables the cutting tool to clear an area of material based on the
boundary of the feature you have selected, then make profile passes around the
feature.
The selected feature is not machined using the Area Clear strategy. A protected area is created
around the selected feature during the machining process.If you have selected Area
Clear, enter a value in the Overcut
Distance box to remove any ridge of unwanted material that might appear
around the feature.
For example, if a Ball
Nose cutting tool is used as the feature tool
with an Area Clear strategy, a ridge
of unmachined material may appear around it:
|
Ball nose tool.
Engraving tool.
Feature allowance
An overcut is necessary to remove this
material. |
The Overcut Distance
should normally be equal to the radius of the Feature
Tool used in an Area Clear
strategy.
- Enter a value in the Allowance box to specify an offset from the machined
vector.
- To perform the machining strategy that you have selected as
a series of passes in the Z direction, select Do
Multiple Z Passes.
- Enter the number of Z passes you want to make in the
Num Slices box.
- Click Linear Spacing.
This distributes the Z passes through the feature material.
- Click Add to add a new
slice.
- Highlight a value in the box on the left of the Do Multiple Passes area and click Delete to delete an individual value.
- Select how the cutting tool reaches the depth you have
defined.
- Drop Tool — If
selected, Carveco checks for collisions between the tool geometry and the
machined relief. This reduces the possibility of gouging.
- Project Tool — If
selected, Carveco ignores the tool geometry and the centreline of the tool is
projected onto the relief.
- Select the Cut Direction
you want to use.
- Climb — Select the
option to rotate the cutter in the same direction as the feed motion. The option
is selected by default.
- Conventional — Select
the option to rotate the cutter in the opposite direction to the feed
motion.
Set the default cutting direction on the Options panel.
- Enter a value in the Tolerance
box to specify how closely you want the cutting tool to follow the shape of the selected feature.
- If you want to change the height at which the tool makes
rapid moves between toolpath segments and define the Home position for the tool,
click the Machine Z control bar to expand its
settings.
- Safe Z — Enter the
height at which your selected tool makes rapid moves between toolpath segments.
This value must be sufficient to clear any clamps used to hold your material
block or sheet in position.
- Home X, Y and Z — Enter
the X, Y and Z coordinates of the tool's start and end position. This should be
a safe distance away from your material block or sheet.
- Click Select next to
Feature Tool to display the Tool Database dialog, from which you can select the
tool you want to use.
- Click Setup next to
Material to define the size of your material
block.
- In the Toolpath area,
enter a Name for the toolpath. If you leave
this box blank, the toolpath is named after the type of toolpath you are
creating. For example, if you create three Feature
Machining toolpaths and do not rename them, they are named Feature Machining, Feature Machining
1 and Feature Machining 2.
- Ensure the vectors along which you want to create the
Feature Machining toolpath are selected,
then:
After you have calculated the toolpath, you can simulate
it.
See also
Related Articles
Creating a recessed feature
Creating a recessed feature Use the Recessed Feature option on the Feature Machining panel to create a recessed (female) feature from a selected vector, usually vector text, which you can then machine using the Feature Machining toolpath. Using the ...
Creating a centre-line engraved feature
Creating a centre-line engraved feature Use the Centre Line Feature option on the Feature Machining panel to create a centreline engraved feature from a selected vector, usually vector text, which you can then machine using the Feature Machining ...
Feature-machining toolpath
Feature-machining toolpath Use the feature machining tool to create engraving toolpaths that take account of the underlying relief. Using the Feature Machining panel, you can: machine a raised, recessed or centreline engraved feature that you have ...
Creating gems
Creating gems Use the Create Gems tool to create a batch of gems, provided that you have already created gem vectors for each of them. When creating gems in this way, a new assembly is also created. To create a one or more gems using gem vectors: In ...
Creating Gems
Creating Gems Use the Create Gems tool to create a batch of gems, provided that you have already created gem vectors for each of them. When creating gems in this way, a new assembly is also created. To create a one or more gems using gem vectors: In ...